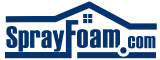
Determining Safe Reoccupancy Times
Without exception, building reoccupancy should be restricted until any spray foam that was installed has cured (fully reacted) and the building has been adequately ventilated and thoroughly cleaned.
To determine a safe reoccupancy time for unprotected workers and building occupants, decision-makers should exercise caution and consult their SPF contractor for specific guidance before the SPF installation. Ask to see any reports developed from product testing on reoccupancy times and the impact of the factors that influence curing variability. Also, read the manufacturer’s recommendation in the material safety data sheet (MSDS), which can be obtained from the contractor or directly from the manufacturer. Note: when determining a safe reoccupancy time, take into consideration vulnerable populations such as children or people with asthma.
Reoccupancy
time depends on curing time, which can vary depending on a number of factors
described below. Per the EPA and manufacturer estimates, reoccupancy time for
two-component high-pressure SPF applications is at least 24 hours, and can be
as long as 72 hours. For one-component low-pressure SPF applications,
reoccupancy can take place after approximately 8 to 24 hours.
Curing Rates Affect Reoccupancy Times
Curing is another way of saying the two chemical components, Sides A and B, are reacting to form polyurethane foam. This does not happen all at once. Indeed, SPF may appear hardened or "tack-free" within a range of a few seconds to a few minutes after the application. However, at that stage, the foam is still curing and still contains unreacted SPF chemicals.
The
curing time–the duration of a complete reaction–depends on a number of factors,
including the type of product, particular formulation, applicator technique,
foam thickness, temperature, humidity, and other factors. Note: cutting or
trimming foam before it is fully cured may cause exposure to unreacted SPF
chemicals.
Air
sampling and testing the indoor air following SPF installation is one way to
assure the foam is completely cured. Testing should be conducted by a certified
laboratory using a validated method, such as the one outlined by the California
Department of Public Health.
In Case of Exposure
If home or building occupants have concerns that they may be exposed to residual SPF chemicals, or continue to smell odors, they should contact their contractor to ensure proper procedures and cleanup were followed. If their concerns are not resolved, affected parties should contact their local or state consumer protection office or contractors’ licensing board. Consumers can also file an online Consumer Product Incident Report with the U.S. Consumer Product Safety Commission.