Into the Depths
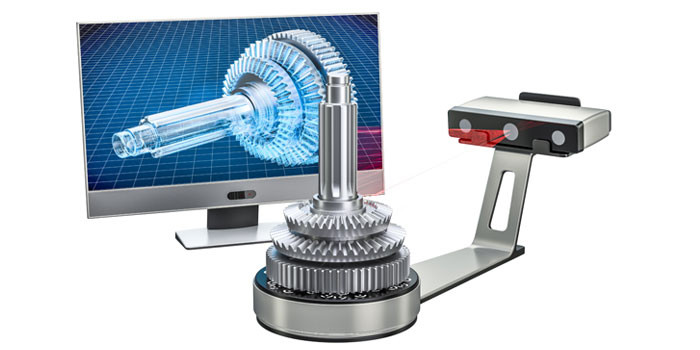
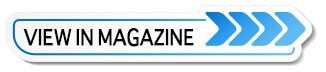
Spray Foam Magazine – Spring 2021 – Note from the author: 3D Laser Scanners could potentially make the sprayer’s job easier by saving them time, improving application quality and Yield measurement. Such an all-encompassing product is not yet on the SPF market for purchase.
How is a manufacturing process such as SPF application done on-site?
It starts with dialing in an acceptable pressure and temperature for the A and B sides, with the help of gauges and transducers. For quality control in some cases (perhaps 10% of machines in the field), the applicator monitors the flow rates using flowmeters for the purpose of monitoring proper ratio mix. Other quality control methods are rarer, such as testing core samples. Therefore, for quality control, we mainly rely on measuring with the use of a depth-gauge (required for R-value assurance). We rely on a tape measure for yield calculation (an indicator of a proper ratio mix) and otherwise rely on the applicator’s experience and comprehensive visual checks for the rest.
So, what’s next?
The possibilities of using a powerful and compact 3D laser scanner: We could observe a wall from 3 feet away and render a 3D mesh as shown below within milliseconds and with an accuracy of 0.1mm. A 3D mesh is basically a 3D map (made from multiple .ply files, more on this later) made up of voxels, pixels in 3D as seen in Figure 1.
Evaluating the 3D mesh using known parameters, reference points, lines, planes, gyro data and some algorithms magic (more on this later), we can calculate the average (mean) depth of the foam within a 0.1mm accuracy at 100,000 locations and all within 100ms. This means that by continuously knowing the depth, the sprayer can adjust his spray technique to maintain an average depth close to his target depth.
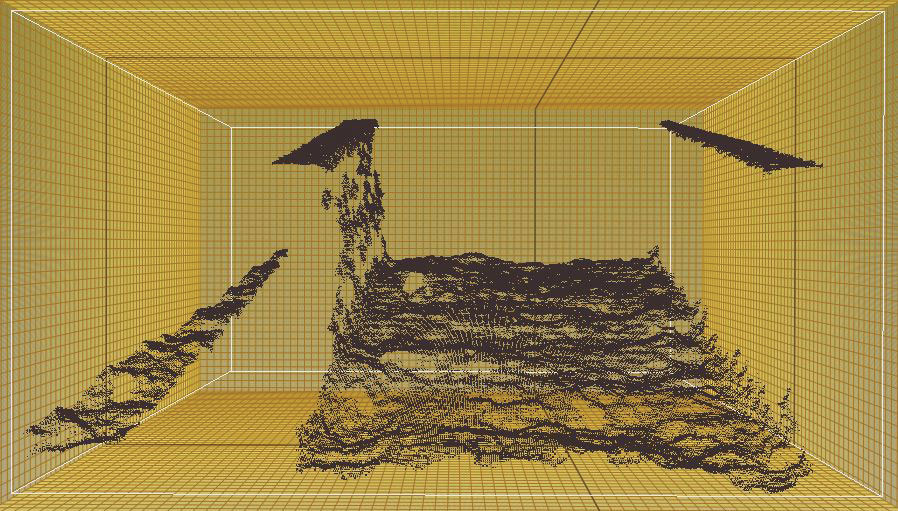
Figure 1
What else could such a tool do?
As you could probably guess, being able to measure area and depth accurately and live user display during the application process, seen in Figure 6, allows for the calculation of yield when the microprocessor is able to read the chemical flow to the spray gun. Having knowledge of yield tells the sprayer if he is optimized for maximum chemical mix efficiency, giving him an indication if the proper chemical reaction is achieved, and allowing more strategic decisions during the workday.
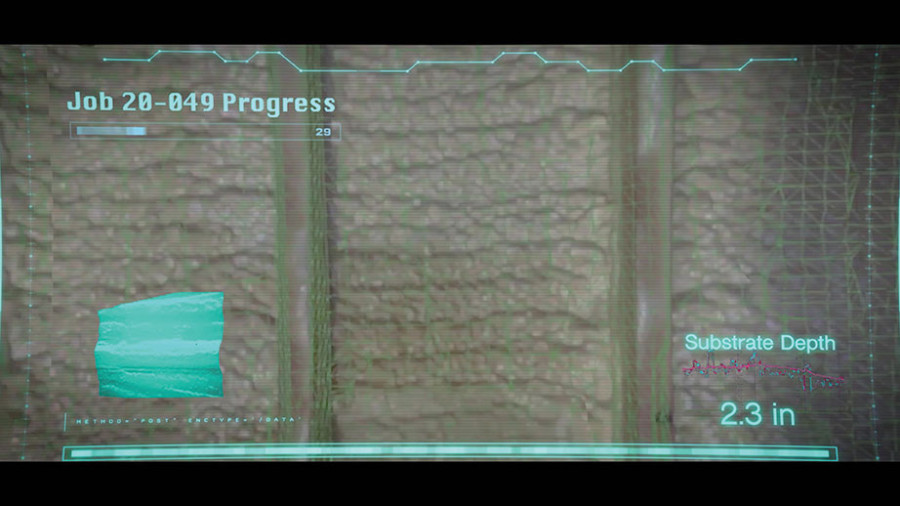
Figure 6
Taking the technology one step further, through the ability to record the 3D mesh surface to such a fine resolution of 0.1mm and within milliseconds, the data can be simultaneously transmitted off-site to a control center, where it can be evaluated and compared with thousands of other 3D meshes from the same chemical foam and with known defects and root causes. An offsite team or central computer can then inform the sprayer if a potential defect was identified and give a recommended fix. For example, two defects sometimes seen in the field are shrinkage and pitting, seen in Figures 2 and 3.
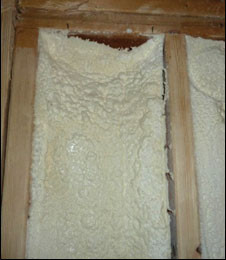
Figure 2
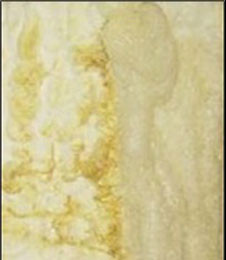
Figure 3
Voxels and vertices are all familiar, because they are used with rendering in computer graphics, for example in a video game, to create an image from a 3D model. Nature solves the “Rendering Equation” by simultaneously reflecting trillions of quantum particles at the speed of light. Physics provides a mathematical model of this (Figure 4.). The contributions of computer science to rendering are efficient ways of approximating and evaluating this model. These include sampling strategies for numerically evaluating integrals, data structures for locating geometric intersections, and processor architectures designed specifically for executing illumination computations.
The resulting Rendering Equation is:

In creating a 3D scan, the opposite is performed. A three-dimensional computer image is created, as shown in Figure 1, based on data gathered from a 3D sensor. There are several ways this can be done; however, most 3D scanning sensors rely on one of five methods: photogrammetry, structured light, laser triangulation, RGB-D, or Time-of-Flight (ToF) technology. Each method has its pluses and minuses.
In general, photogrammetry is fastest with the lowest cost. Structured light and laser triangulation provide highest resolution and detail. RGB-D and ToF provide a good mix of speed and cost, although with lower resolution. One application using the ToF is LIDAR (Light Detection and Ranging.) First used on the Apollo 15 mission in 1971 to map the surface of the moon, it is now found in some high- end mobile electronics such as tablets. Some 3D sensors also record accelerometer and gyroscope data using an IMU (Inertial Measurement Unit.) When data is combined from continuous 3D scans or ply files (Figure 5), we can create, for example, a final mesh representing an entire attic substrate with fully expanded and fully applied SPF between the rafters.
What does the algorithm’s magic look like?
By evaluating foam as it transitions from liquid to semi-solid, then to solid, expanding and then contracting takes some data manipulation. We also must “filter” out studs, windows, plastic, and any other foreign objects (including the sprayers hand and spray gun.) All are moving in three dimensions relative to the sensor, which captures coordinates of ten million voxels per second. One great advantage that we have however in SPF is that we do not need to display a complex image requiring a GPU because we need to primarily crunch data for the purpose of presenting the results to the user in text format, thus allowing for more computational power where it is required. For measuring substrate depth, we also do not require an accuracy of 0.1mm. Even 1.0mm is adequate.
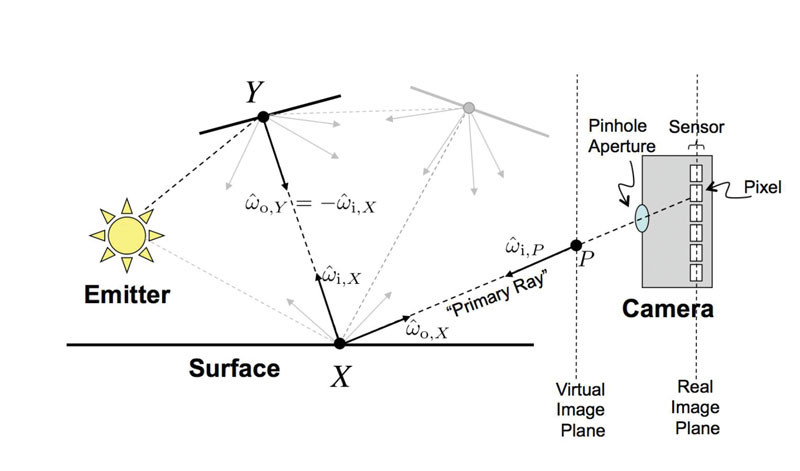
Figure 4
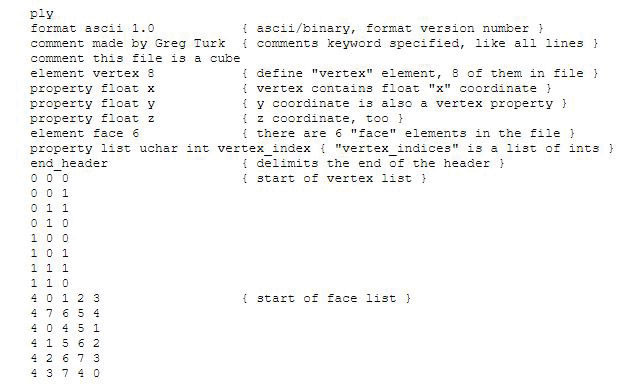
Figure 5
And voila, the sprayer now knows that maximum yield has been accomplished, and the application is not too deep or too shallow and the foam is free of suspected defects.
3D laser scanners are new technology, and this tech is evolving fast. Imagine a compact printer as small as your finger, that is the future. Like all new tech, the current 3D laser scanners are on the pricey side but as the tech develops and the sizes decrease then so will the price.
If a customer has a choice for their $10,000 foam job between a contractor who shows easily with quantifiable data that the job was sprayed at three inches, and with proper yield and another contractor without this technology, who will they choose? Most likely the contractor with the “quality assurance” aspect. The 3D Laser Scanner market in the U.S. was estimated at $621.7 million in the year 2020 with continued accelerated growth predicted. Let’s hope this revolutionary piece of technology can be made part of our industries future advancements.
Direct any questions you have about statements made in this article to Daniel Dorneanu: dan@psftechnologies.com
ABOUT THE AUTHOR Daniel Dorneanu is the owner of Palmetto Spray Foam Insulation in Charleston, SC where he lives with his wife and two wonderful children. He is a retired Bosch engineer with a Mechanical Engineering degree and an Electrical Engineering degree from GMI Engineering and Management Institute. He is an author of two U.S. patents in the SPF industry and a proud member of SPFA Technical Committee. He is always glad to help other sprayers in the industry.
Disqus website name not provided.